Improve quality, CS
Improve the quality and customer satisfaction (CS)
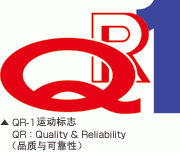
Sumitomo electric industries would have started to pay attention to scientific management, obtain the deming award in 1962, started in 1975 in the whole company launched "improve reliability movement" movement, and then to the "quality" and "reliability" as the center, according to the situation of different period, setting the corresponding key issues in the whole company quality reliability activities.
, on the basis of these results to accumulate, sumitomo electric industries since 2002, in "do the best enterprise customers eyes" slogan, to realize the goal of quality in the world to carry out the QR - 1 movement, and the "customer" and "attention quality" as the quality index of the two pillars.Sumitomo electric group most of the business is related to customer business (B to B), only to master in the daily business activities such as customer's opinions and requirements, attaches great importance to further improve the quality, can achieve the goal of satisfying customers.
Launching a campaign QR - 1
Since 2013, QR - 1 activity has always been to "through the engineering activities' challenge processes zero defect" as the slogan, in global scale.Back in each working procedure in the "no manufacturing, no flow defect products," the basic position, product forms at home and abroad in Japan, the condition of different nonconforming product factory to establish a clear pass/defect judgment benchmarks.Our goal, it is within the source of customer complaint - manufacturing process quality not qualified or abnormal, quality defect occurs immediately grasp the situation, and the challenge to completely eradicate it, so as to make improvement in system level and culture level.Object of this activity is not limited to the production department, the department of production technology, product design department will also participate in together, in order to "production chain downstream is same customers" way of thinking, build establish manufacturing, strong physique of current defect products.
Inspection to improve quality and support
From the perspective of the customer to evaluate the quality of the department activity, and the quality management activities and weak links on the structure of the quality management to improve.(structure) levels in order to improve the quality assurance system, the important base of every enterprise headquarters in a planned way to promote "quality inspection" in the world, at the same time, in the event of a major complaint, the complaint department for inspection at any time.In global quality inspection, from the viewpoint of management, design, manufacture, clear the weakness of organization system, to physical improvement activities as an opportunity, to assist the part weak support.
Raise awareness of the quality of every employee
Group is committed to promote all the staff to understand the leadership way of thinking for quality, improve staff quality consciousness.Therefore, the group adopted a number of measures.For example a company-wide quality meeting;To carry out the quality on the quality of activities to strengthen;At the start of annual and other important time node through company publications, such as internal radio presidents message;Leadership field trips, and so on.These measures will be in the ascension of the awareness of quality work.
In addition, the group also has a character recognition system.Good performance in the production activities, can be an example to other sectors of the department, or the year posters quality slogan, quality of outstanding works, will be in the whole company recognized quality meeting places.
Improve the ability of individual education
Sumitomo electric industries in order to further improve and stable product and service quality, make every employee improve the level of business quality is important, therefore, to implement employee training education activities at the university of SEI.At the beginning of each year, completes the annual education quality improvement plan, is an object with all the staff, according to different levels, different departments and different positions respectively adapt to every function and position of education, and meet the demand of knowledge of special education.To meet the requirements of each department, QC management tools to use, "improve the real reason for force", by visiting the relevant departments, the implementation of the "academic" of the door.
In addition, in terms of product safety, and legal department to be held once a year the manufacturing material liability law (PL) and the revised "the consumer products safety law (revised consumer products safety act) of the professional training.List to all group as the object, through recent examples, to deepen the understanding of the laws and regulations, at the same time in terms of product safety reviews, a warning on the safety of products such as confirmed that collect information about product safety and accident countermeasures such as practical training.
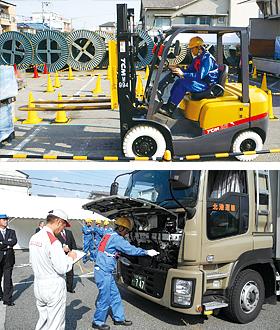
Logistics quality improvement initiatives
Sumitomo electric industries in order to prevent the products in the process of transportation accident (cargo damage or dirty, etc.), accurate product into the hands of customers, and the carrier transport company together, in order to improve the quality of logistics.
Especially of damage caused by forklift, accounts for nearly half of products in the process of transportation accidents, in order to reduce the accident, and will note the point together forklift related basic operation, specially produced a video teaching material, not only within the company, associated company, but also provide the transportation company and associated companies use.In addition, also took various countermeasures, in order to improve the driver's driving skills, for example, hold "basic driving forklift truck operation competition", etc.
Business department to improve customer satisfaction (CS)
The group doing business in a wide range of areas, except a tiny fraction of end products, basically belongs to the category of the B2B.In the daily sales activities, such as link accurately grasp the customers' opinions and demands (enterprise), continuously improve the quality of products, and is the necessary request to improve CS (customer satisfaction).
Therefore, the group will to investigate sales ability is an object with sales director.
Specifically, sales at the head of the customers as the object, through questionnaire investigation at ordinary times satisfaction with the sales activities, and evaluation of results.
Evaluation results will be feedback to the sales person and supervisor.To encourage, encourage sales to raise their selling my capacity at the same time, the overall evaluation results will also be adjusted education, guidance method is an important reference.In this way, the level of the sales department will be strengthened, CS will get promoted.